こんにちは、ヒロアキです
今回は、実際に30MMシリーズ用のカスタムパーツをモデリングして、3Dプリントまでしてみようと思います
前回までにキャリブレーションと3mmジョイントの寸法テストを行ったことで、精度に関しての基準ができました
それを元に、いよいよカスタムパーツの制作に入っていきます
① まずは写真を撮る
カスタムパーツを取り付ける予定の30MM機体を、できるだけ正面から撮影します
斜めや角度がついていると、後の作業がやりにくくなるので注意です
② 完成予想図を書き込む
撮った写真に、ざっくりと完成イメージを書き込んでいきます
自分はWindows標準の「ペイント」を使っていますが、線が引ければ何でもOKです
ここでのポイントは、凝ったデザインにしすぎないこと
これはあくまで全体のバランスを見るための下書きです
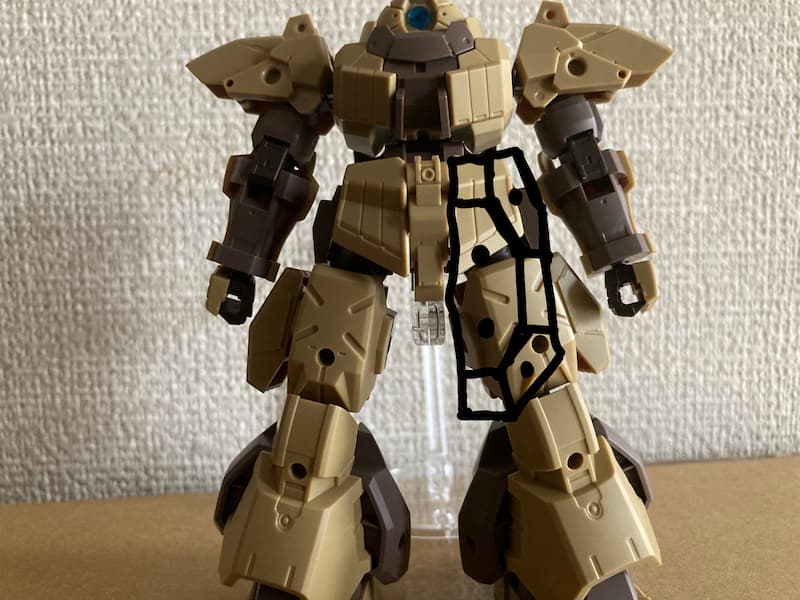
③ Fusionに読み込んで設計スタート
書き込んだ画像をFusionに読み込みます
その際、実際に作る予定の縦のサイズを事前にメモしておきましょう
- Fusionに画像を挿入
- 左のキャンパスにある画像を右クリック → 位置合わせを選び
- 一番上と一番下をポインターで指定して、さきほどメモしたサイズを入力します
これで画像の大きさを実物に近づけることができ、精度の高い設計がスタートできます
④ スケッチで清書する
先ほど作成した完成予想図を参考にして、Fusion上でざっくりとスケッチを引いていきます
この段階で、きれいに清書して形を整えましょう
ただし、あまり細かい部分にこだわりすぎなくても大丈夫です
作っていくうちに「ここ、少し変えたいな… という箇所が出てくるのは普通なので、柔軟に考えてOKです
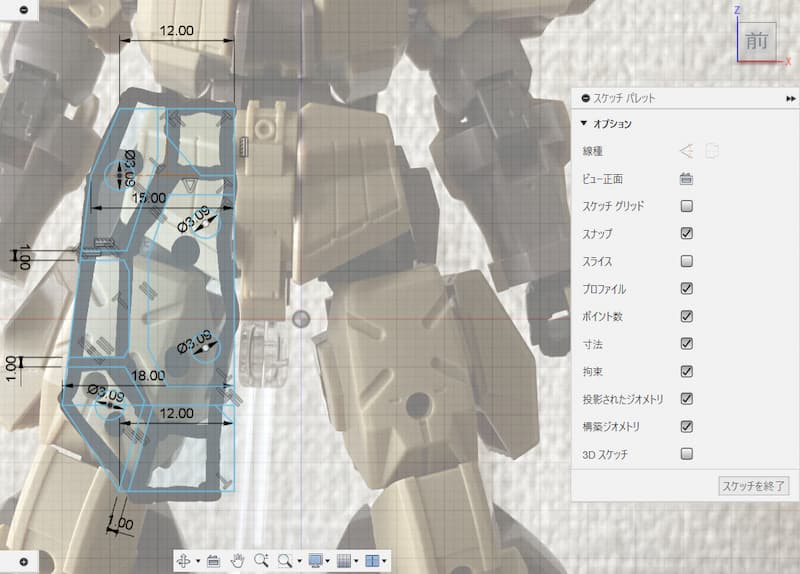
⑤ 押し出して形を作る
スケッチができたら、すべて選択しておおよそ4mmほど押し出します
この押し出したパーツがベース(土台)になります
※もちろん、4mmという数値は目安です。
後で取り付ける3mmピンを考えて、ある程度の厚みが必要なので、それを意識して厚みを決めましょう

⑥ ディテールを加える
ベースができたら、さっきスケッチしたのでさらに押し出したり、穴をあけたりしてディテールを追加していきます
自分は、立体感のメリハリを出したいので1mmほど押し出して段差をつけました
ここは完全にお好みで調整してOKです
そして出来たものがこんな感じ
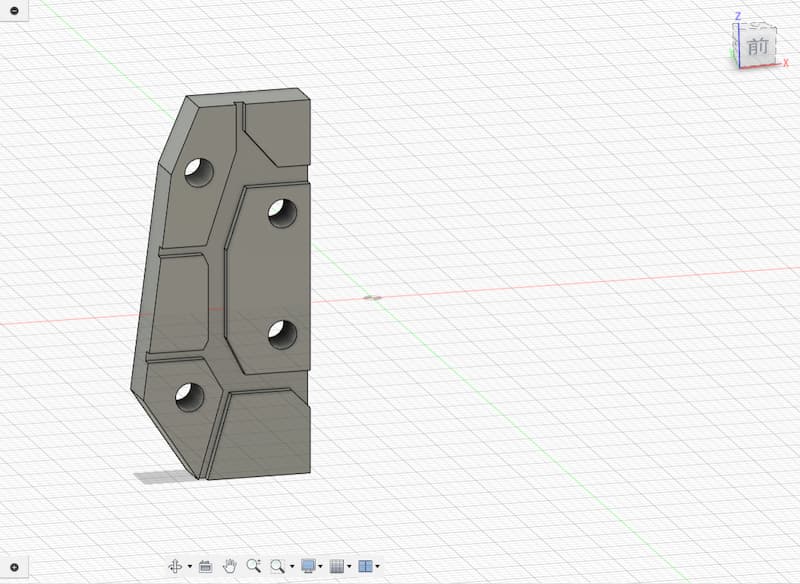
⑦ 傾斜を作成
現在のモデルは平らな形状なので、下の部分に少し傾斜をつけて立体感を出していきます
このひと手間で、見た目がグッと良くなります
まず、側面ビューで斜めのラインをスケッチします(下方向に削るようなイメージです)。
この斜めのラインをスイープの断面(プロファイル)として使うため、次にスイープのパス(経路)を作ります
正面ビューで新たにスケッチを作成します
「投影(Project)」機能を使って、ベースの輪郭をスケッチ上に映し出します
映し出した輪郭をオフセットして、スイープ用のパスを描きます
※オフセット量はお好みでOKですが、今回は0.4mmで設定しています。
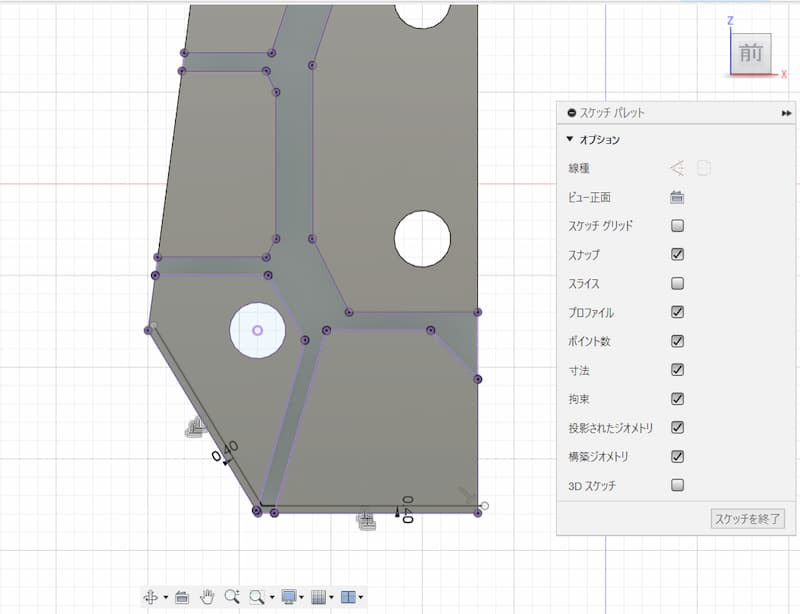
サーフェス → スイープを使って、先ほどの断面とパスを元に傾斜面(サーフェス)を作成します
そして作ったサーフェスを使って、「ボディ分割」を実行します
これで、下部に傾斜をつけた形状が完成します
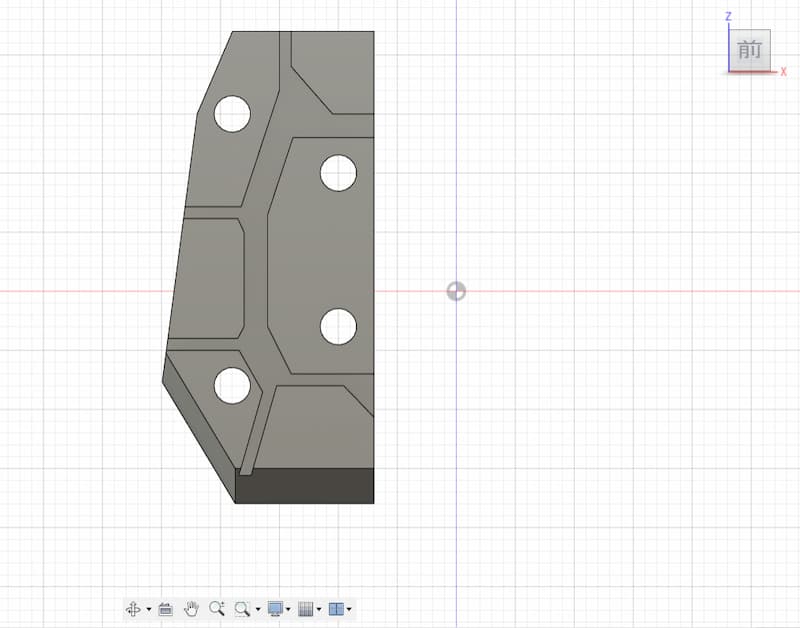
⑧ 接続用の3mmピンを作成
最後に、腰部に取り付けるための3mmピンを追加します
今回は長さ3mmのピンを作りましたが、取り付ける30MM本体の構造によっては長さが異なる場合もあるので、事前にしっかり測っておくことをおすすめします
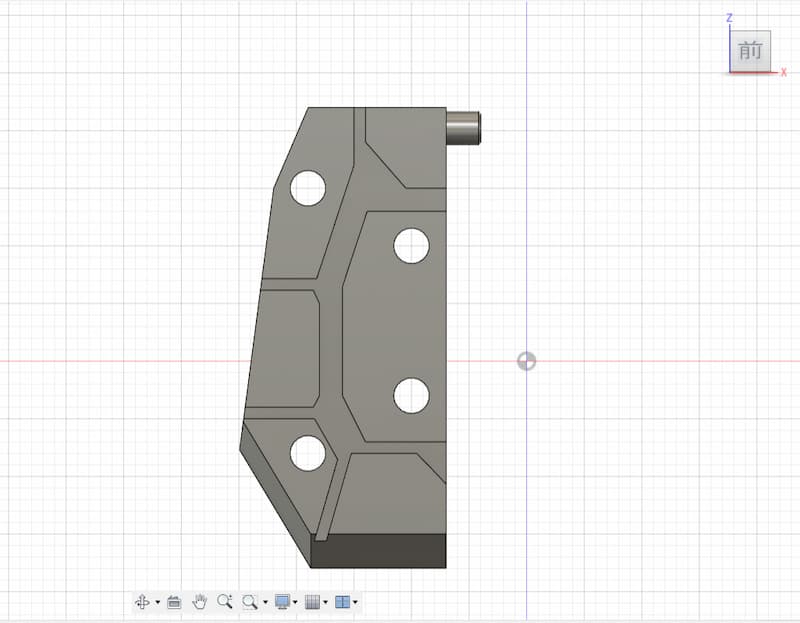
⑨ シェルで肉厚調整
ここまででデザインとしては完成です。
次に、「シェル(Shell)」機能を使って内部を中空にし、3Dプリント用に適した厚みにします
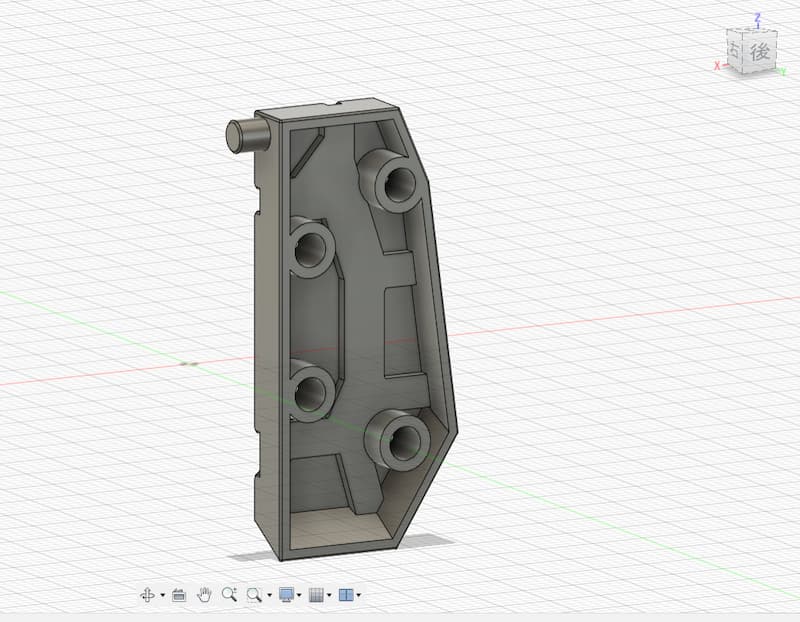
今回は30MM用のシンプルなデザインとして、ディテールはあえて控えめにしましたが、
・装甲のディテールを追加する
・フロントアーマーの裏側をしっかり作り込む
といったカスタムも十分アリだと思います
⑩ ミラーで左右対称に仕上げる
最後に、「ミラー」機能を使って反対側のパーツを作成します
これで左右対称のモデリングが完了です
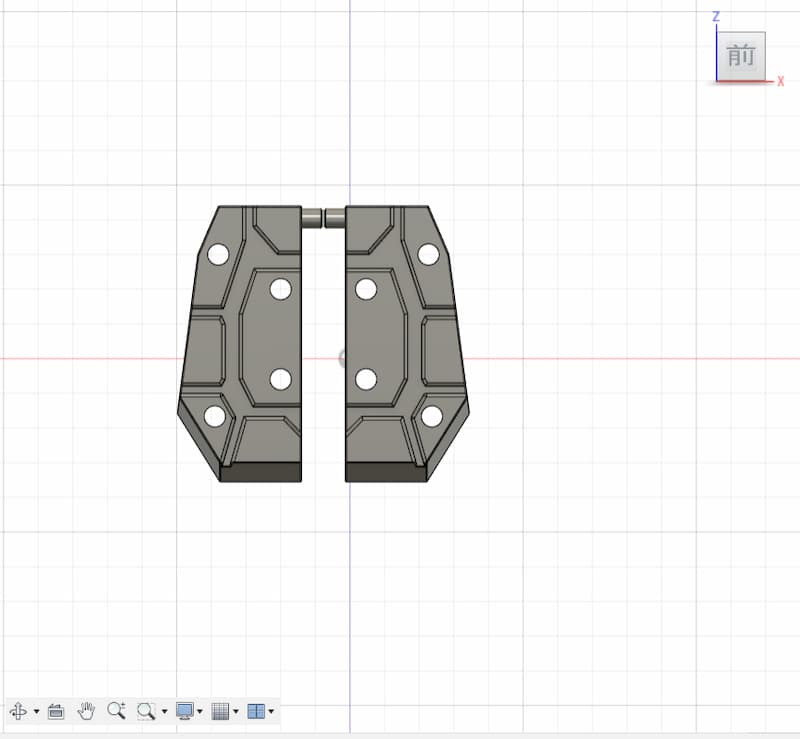
念のため、キャンバス上に表示して最終確認をしておきましょう
・バランスは崩れていないか
・機体と自然に馴染んでいるか
などをチェックします
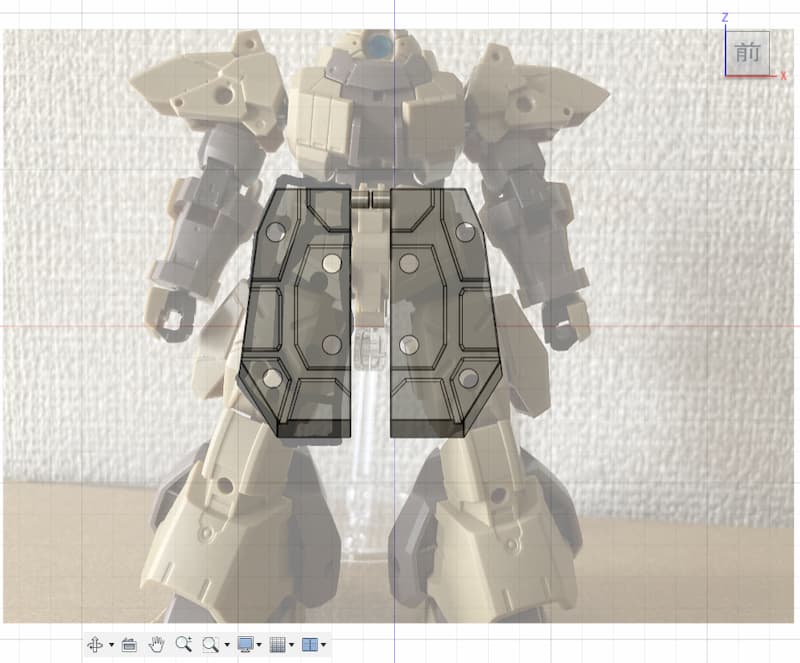
⑪ いよいよ印刷!
問題がなければ、いよいよSTLとして書き出して3Dプリントに移ります
ここでワンポイント
時間に余裕がある方は、まず片側だけ印刷してみるのがオススメです
なぜかというと、実際に作ってみると
「なんか違う……」
という“コレジャナイ感”が出てくることがあるからです
一度印刷して確認することで、不要な出力の無駄を減らすことができます
もちろん、デザインに自信がある場合は両側同時に印刷しても問題ありません
完成
こちらが今回制作したカスタムパーツです
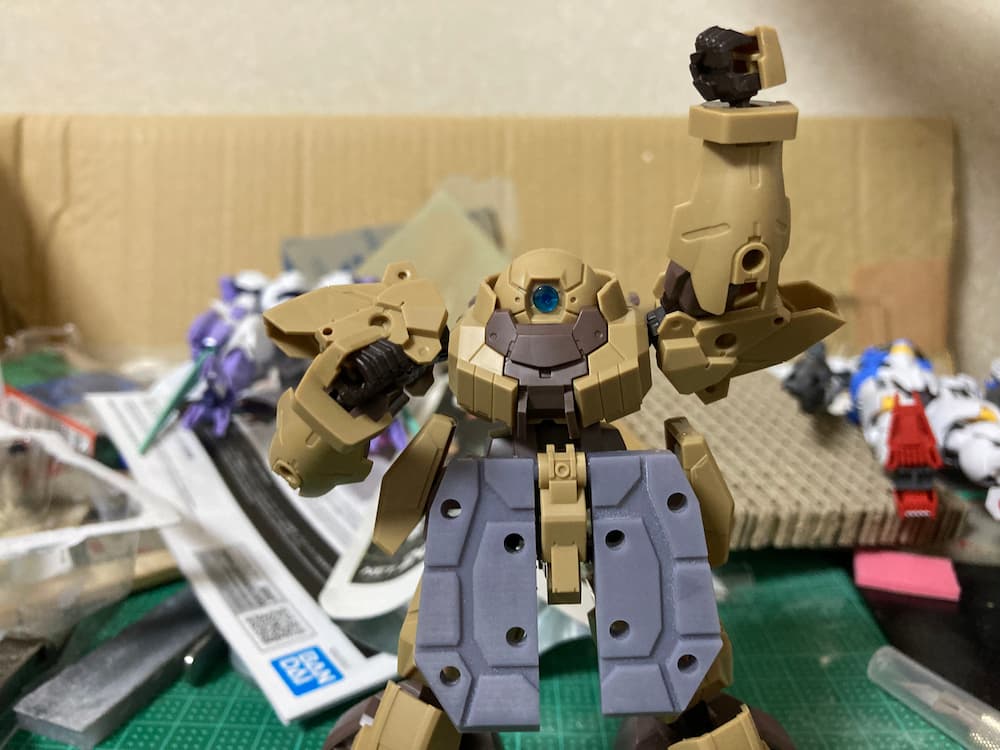
3mmジョイント対応の穴を設けているので、30MMのさまざまな部位に取り付けて遊ぶことができます
たとえば、こんな感じで装着できます
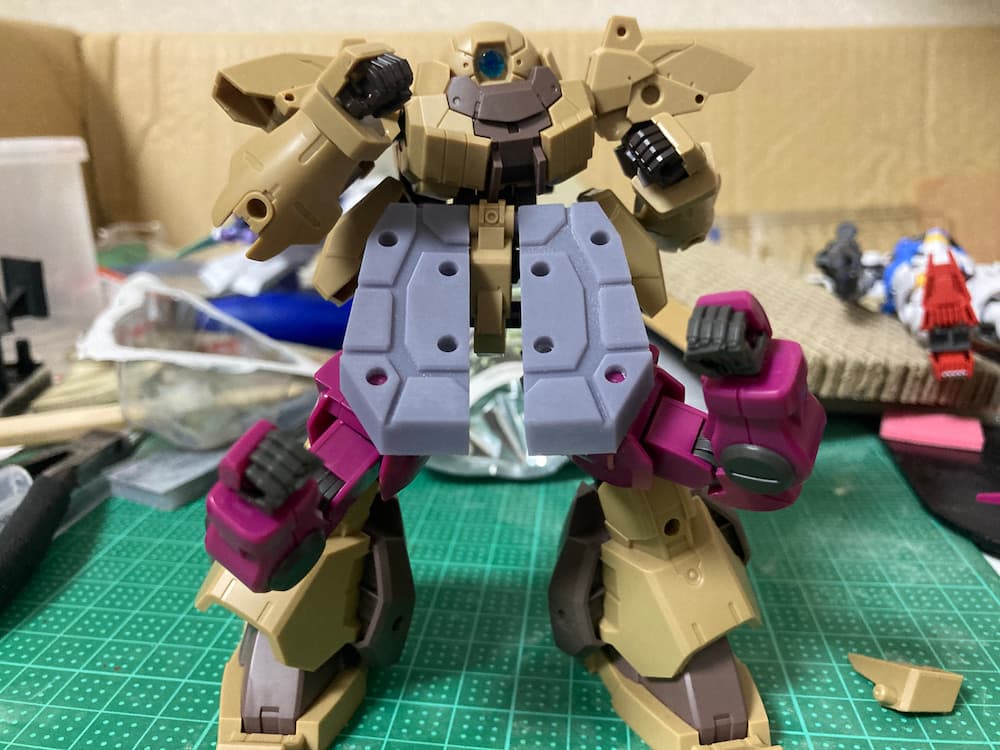
カスタムの幅が一気に広がるので、組み換えやポージングがますます楽しくなります
まとめ
今回は、写真から完成予想図を描いて、Fusionで設計し、3Dプリントまで行う一連の流れを紹介しました
特別なツールや複雑な設計技術がなくても、
「やってみよう」と思えば自分だけのカスタムパーツが意外と簡単に作れます
30MMはカスタムの自由度が高いシリーズなので、こういった個人製作のパーツとも相性抜群です
この記事が、皆さんのカスタム製作のヒントになればうれしいというお話